 |
company profile

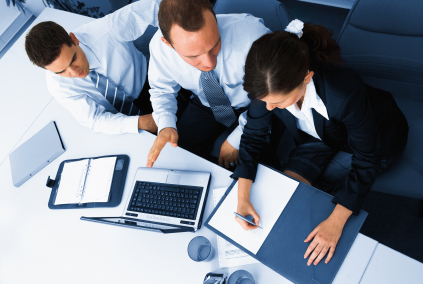
Product Development & Analysis (PDA) was started by leading industry professionals over 27 years ago with the goal of being a one stop solution provider of state of the art design, development, validation, analysis, prototyping & low volume contract manufacturing and contract research for defense, transportation, power generation, medical, and general engineering sectors.
PDA has grown over the years into just that. We are very proud of the multitude of projects we have undertaken and the wide range of industries we continue to be serving.
Recently, PDA has expanded their services in the areas of Data Mining and Analytics, problem solution using Machine Learning and AI technologies including Digital Twins and Industry 4.0 adoption in the metal casting industry.
|
 |
|
 what we do

|
Providing engineering and manufacturing services.
Product Development & Analysis (PDA) has combined over 60 years of experience in metalcast, plastic and FRP composite product development, redesign, and reverse engineering Using CAE techniques, 3D Digital Scanning, Additive Manufacturing and Rapid Prototyping tools. PDA has been a virtual partner - providing innovative, integrated design, development, value engineering and manufacturing solutions and tools to the US Military, OEM's and tier suppliers.
|
PDA also partners with professional societies and OEM's to develop innovative materials, tools and processes using government-funded contract research and development.
|
PDA has experience in new product development, reverse engineering, fab to casting conversion and redesign of over 750 components with varying complexity. PDA offers failure analysis, problem solving, cost reduction, quality and performance improvement, and optimization using a combination of knowledge base, experience, CAE and Data Analytics (ML/AI) tools.
|
Computer Aided Engineering tools (CAE)

|
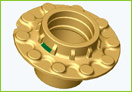 |
Computer Aided Design CAD
Product Development & Analysis (PDA) uses CAD tools to develop your product concept from the drawing board to manufacturing. PDA is able to design and develop complex solid models (rough casting, tooling and finish machined), sub-assemblies and assemblies from ideas and sketches. 3D prototypes and 2D manufacturing drawings are digitally created to get products to the market efficiently.
|
|
|
|
Finite Element Analysis FEA
PDA has the ability to perform product design and performance validations using its FEA tools. PDA specializes in FEA-based tests and evaluations for the shock, vibration, static and dynamic loadings, impact, transient thermal as well as linear and non-linear structural analysis. Whether your product is in the design phase or you?re looking to increase the life and/or performance of an existing product or conduct a pre-qualification before functional test and evaluation, PDA's Finite
Element Analysis experts are there for you. FEA allows our experts to run products thru a wide variety of severe conditions that they may experience during their lifetime. FEA also allows optimization of products e.g. weight minimization. Suggestions or changes are then made to increase the overall functionality of the product.
|
|
|
|
Computational Fluid Dynamics CFD
Using its CFD tools, PDA has the expertise to perform product and system performance validations, such as fluid thermal interactions. CFD tools allow us to model the air and other fluid flow throughout the system. If required, it can be coupled with thermal boundary conditions to stream line and optimize the end performance. The tool also enables us to simulate flow driven motions, flow behaviors of rotating elements such as fan blade and impellers, as well as
turbulence and non-Newtonian flow modeling. CFD allows us to model natural and forced convection problems, such as electronic packaging and heat sink. Our trace particle animations allow engineers to visualize the flow path very clearly.
|
|
|
|
Manufacturing Process Modeling
When it comes to cast metal, plastic and composite components; part geometry, tooling design and process parameters are key to ensuring an optimum design, a quality part with minimal scrap, higher reliability and reproducibility. PDA pioneered the use of Casting Process Simulation as a tool for Concurrent Product and Process Development (CPPD) and has the expertise to design and validate the expensive tooling, there by, eliminating the rework cost and time
delays with traditional trial and error approach. PDA also often uses the Process Simulation as a Problem Solution tool to improve the quality of an existing cast part, yielding cost reductions. |
|
|
|
Additive Manufacturing of Sand and Investment Castings
PDA has been providing solutions including design for additive manufacturing of complex sand and investment castings using tooling free 3D printed sand mold & core and wax patterns in various alloys with greater complexity and no size restrictions. We specialize in developing the complex casting design by consolidating multi piece cores, features and parts into one piece configuration, select the alloy, develop the rigging and process parameters and validate with advance simulation to produce either prototype or low volume castings eliminating the need for any tooling related cost and time.
|
|
|
|
Data Mining & Analytics using Meta Modeling w ML/AI Techniques
PDA has added expertise in solving complex multi-dimensional metal casting design, physics based advance simulation and manufacturing issues such as scrap due to shrinkage porosities & non-compliant property requirements, in near real time by analyzing the historical data, identifying key variables, running Design of Experiments, and building meta models (emulators) using modern machine learning and artificial intelligence techniques specific to their operation and processes.
|
Learn More about Our Success Story 
|
|